A leading developer and supplier of advanced, interoperable tactical and enterprise communication systems approached Sherpa with an interesting challenge: reimagine their current power supply subsystem design to allow for higher power applications – within the constraints of the current envelope.
What made both possible on a tight schedule: redesigning the product for additive manufacturing with Carbon DLS technology.
Exploring beyond traditional manufacturing
The existing air duct had been designed for manufacturing with sheet metal and featured vertically mounted impeller fans for cooling. While functional, those fans had limited cooling abilities. This became an issue when end users would rely on the power supply for the operation of server or network equipment under higher ambient temperatures.
To begin to explore new possibilities, our client’s team developed a rough concept for a four-axial fan-based cooling system. Informed by flow simulation studies, they had redesigned the duct’s louvers to more accurately direct air where it needed to go. With these more complex louver shapes, the duct would be difficult to manufacture with traditional methods.
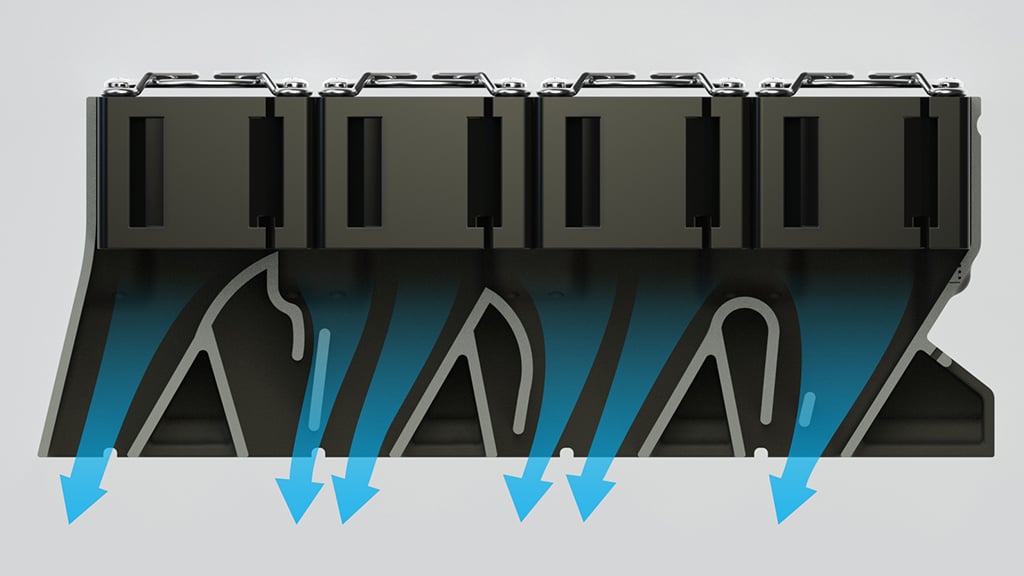
Redesign for efficiency and durability
Our experts at Sherpa redesigned the duct components for Carbon DLS printing technology and then prototyped them for initial testing. In this process, our team was able to reduce the initial concept design cost by 50%.
From here, our client evolved their concept into a longer five-fan version. Our team identified the optimal production approach as a two-part print, fastened together without obstructing airflow. With the resolution of our Carbon M2 printer, we were able to create a V-shaped profile at the seam that minimized air leaks and precisely aligned the two halves.
For production, we selected the EPX 82 resin for its functional toughness and thermal stability. As part of the product assembly, it passed military standard testing MIL-STD-810H.
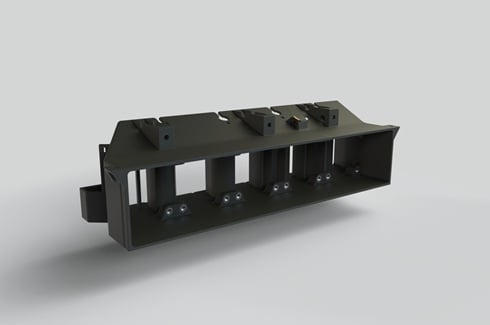
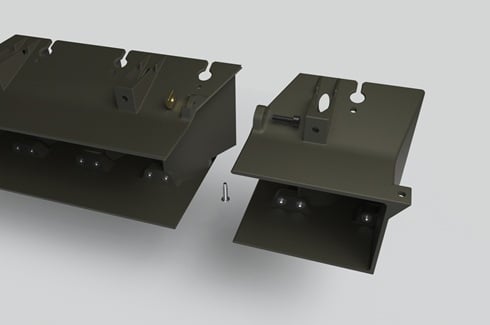
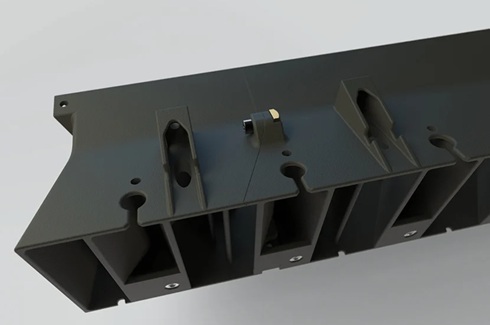
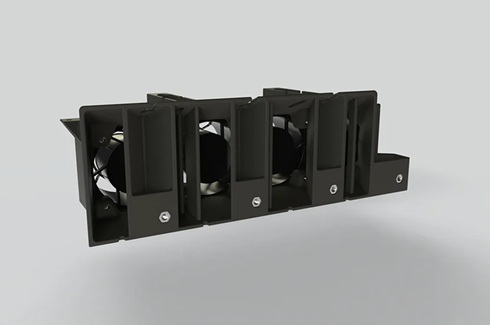
Greater performance and agility
The new air duct design allowed the power supply to perform under ambient temperatures 10 °C above the previous iteration.
Finally, using Carbon DLS printing technology accelerated the process from concept to functional prototype and brought the project to the production stage much faster than traditional manufacturing. It also gave us flexibility to quickly respond to design updates.
What that means for the end user: more power and better performance within a familiar form.
Isotropic Properties
One of the challenges for this part was that it needed to include threaded inserts. Carbon DLS printing is known for its high isotropic properties.
Unlike many 3D printing processes, Carbon DLS produces parts with uniform strength across all directions, making them ideal for applications with complex loading patterns. This allowed us to install additional hardware, like the threaded inserts, with confidence. Using the same resin as the printed part, we can create similar results to insert molding.
We looked at and tried many threaded inserts, until we found the best one for our purpose. We then decided to perform a stress test to make sure the inserts stay in place, verifying they meet the customer’s requirements.
The Stress Test
A stress test was designed for testing the breaking point of a fixture. We used our in-house Mark 10 motorized force testing machine. It has a range of up to 500 pounds of force. The results were excellent, giving us a huge safety margin over the requirements provided by the customer. We observed three failure modes, all with a max load of well over 100 pounds of force.
Constant Improvement
Once we printed parts, we provided to in-house assembly before shipping them to the customer. This was a long-term client, and we are always looking for ways to streamline our processes and save our customers.
One of the first things we did was review ways to streamline the assembly process. We did this by creating a fixture that would hold the parts down so the threaded inserts could be installed quickly.
The New M3 Max
The next big improvement came with our purchase of the new M3 Max Printer. Up until now we printed the unit as two parts, which we would then assemble. The M3 printer comes with a larger build volume which enabled us to print the unit as one part. This made it cheaper to produce per unit as well as being stronger and easier to assemble.