Thermal Imaging Display for Pilots
When Max-Viz, an aerospace company dedicated to developing Enhanced Vision Systems for the aviation industry, needed support for their first product, the EVS 100, they turned to Sherpa Design. The goal was to extend a pilot’s forward vision by at least eight times what the naked eye could see in challenging weather conditions or during nighttime flights. This thermal camera design will have a significant bearing on a pilot’s ability to negotiate a survivable landing during an engine out at night or in dense haze.
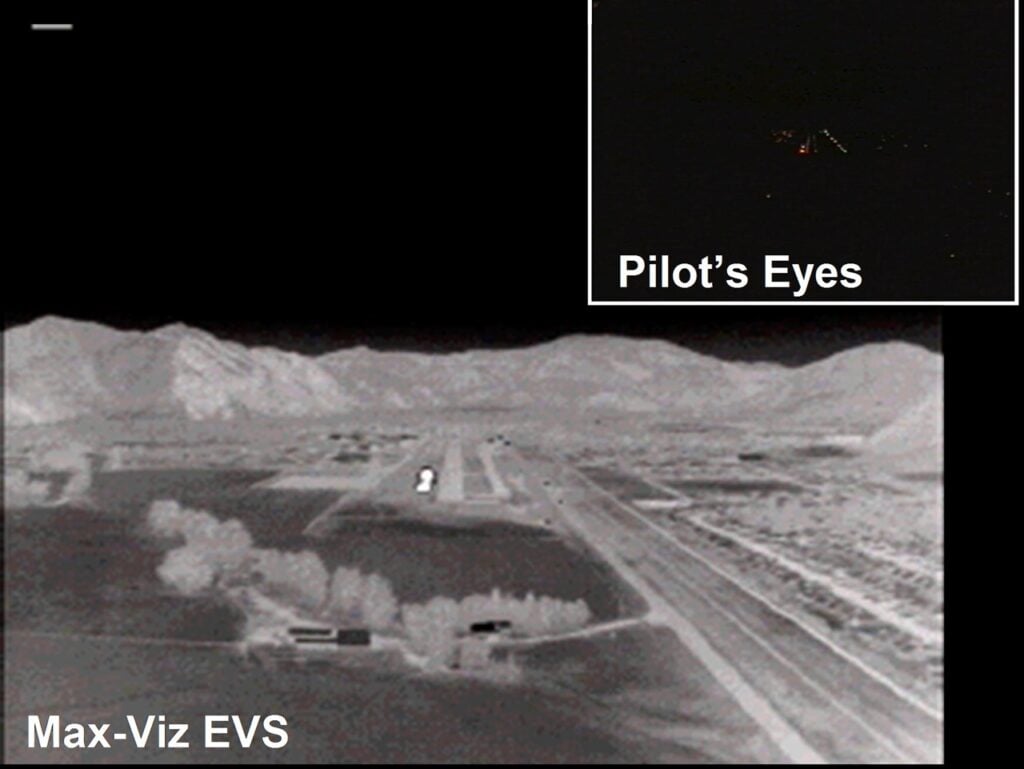
Design Challenge
Max-Viz had already acquired a military-grade thermal imaging camera, licensed an uncooled focal plane array, and developed a patented system to fuse video images. They needed our expertise in industrial design and mechanical engineering, integrating these components into a sleek, aerodynamic housing that could be mounted on various aircraft. The challenge was to create an enclosure that not only met strict size requirements, but also offered optimal performance under diverse operational conditions.
Product Requirements Document
The Product Requirements Document specified the enclosure should be a self-contained aerodynamic pod, with a sleek design and an overall size of approximately 9” long and 2.3” in diameter. It needed to be waterproof and function well with an operating temperature range of –55C to +70C.
The “camera” is a hermetically sealed package that undergoes a dry nitrogen purge to prevent moisture and dust from entering the sensors. Integral window heaters are to be included to prevent ice buildup, and a sun sensor added to protect the unit if the aircraft is pointed toward the sun. The system should be set up to run independently, minimizing impact on pilot workload.
The pod will mount to the aircraft above or below the fuselage or wing, like a pitot tube. It may need to be mounted to areas of the aircraft that have unique surfacing regions. Therefore, the pod assembly would need to utilize a customized top ‘adapter’-mounting strut for the different ways it can be mounted.
SPEC REQUIREMENTS
- Package:
- Sealed and purged with dry nitrogen positive pressure.
- Self-contained aerodynamic housing, ~9” L x 2.6” W x 2.0”H
- Molded plastic or cast aluminum.
- Mounting:
- On top of the cabin
- Environment:
- No degradation when exposed to UV.
- -55 to +70 degrees centigrade
- Waterproof
- Flammability:
- Per DO-160E, section 26
- Resistivity:
- < 5 K Ohm-cm
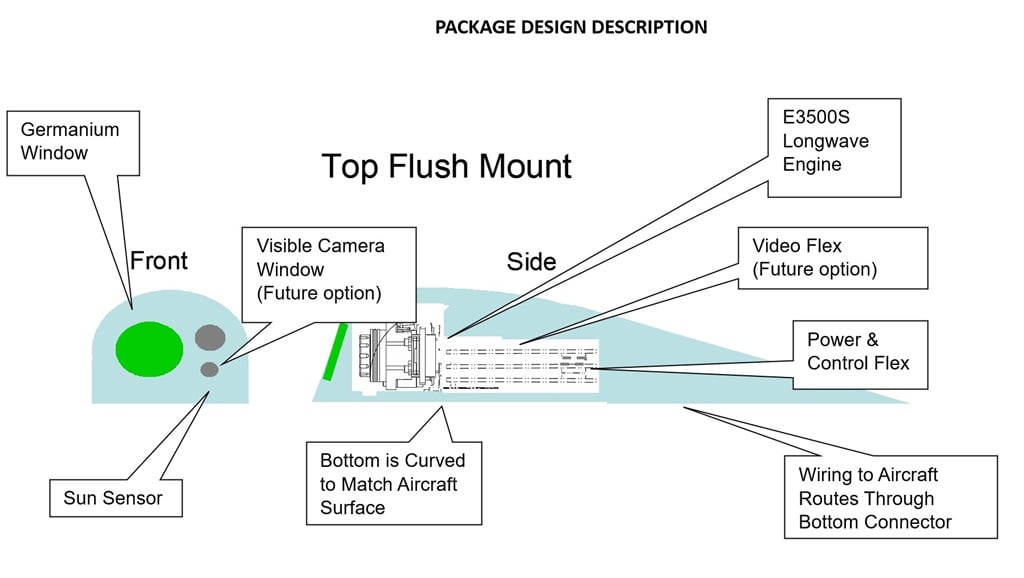
Thermal camera housing design
Sherpa developed a conceptual layout of the pod assembly and defined space requirements for the components. This included integral window heaters that prevent ice buildup so the thermal camera can deliver images in low temperatures without defrosting.
Looking directly into the sun would damage the infrared camera and so Sherpa needed to design a way to protect the camera during ascent. A sunshade was designed that would cover the camera and a sun sensor placed at the front of the housing which would activate the shutter whenever it was hit by direct sunlight.
Sherpa designed and built the enclosure, the camera support structures, and integrated the boards and connectors.
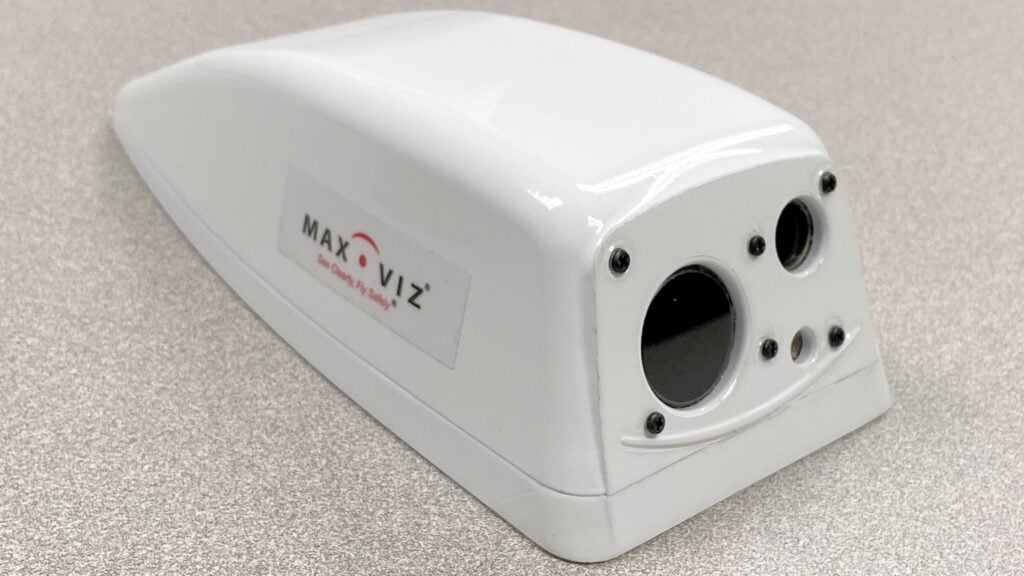
Early in the design process, Sherpa worked to identify the material that best satisfies the performance and cost requirements. Molded plastic or cast aluminum were the two materials being considered for pod housing material. We ended up going with molded plastic to keep costs down, but that meant it needed additional RF shielding paint added to it.
Biggest Challenges
One of the biggest challenges in the design was getting an airtight seal on a plastic enclosure. Sherpa solved that by working with different material suppliers to find the best plastics and by developing custom o rings which utilized o ring grease.
Another obstacle was designing a base plate that could fit different locations on various planes. The plate needed to be flexible so it could be adapted to many different aircraft. We developed it like a block on the base of the unit, allowing you to trim the profile from the base plate. This made it easy to develop the product to fit a new model of aircraft or new location on an aircraft. Once shaped it could easily be injection molded for production runs for that placement and style of airplane.
Design for manufacturing
Sherpa is committed to delivering not just innovative designs, but designs that can be manufactured efficiently. We detailed the assembly design for the enclosure, circuits, and components, refining SolidWorks models and performing necessary analyses to ensure functional excellence. Working closely with Max-Viz’s manufacturers, we developed assembly drawings, BOM (bill of materials), and part drawings needed for FAA submission.
First Plane FAA Certified
Sherpa successfully developed the base plate and got it mounted and operational on the first plane, a Cessna.
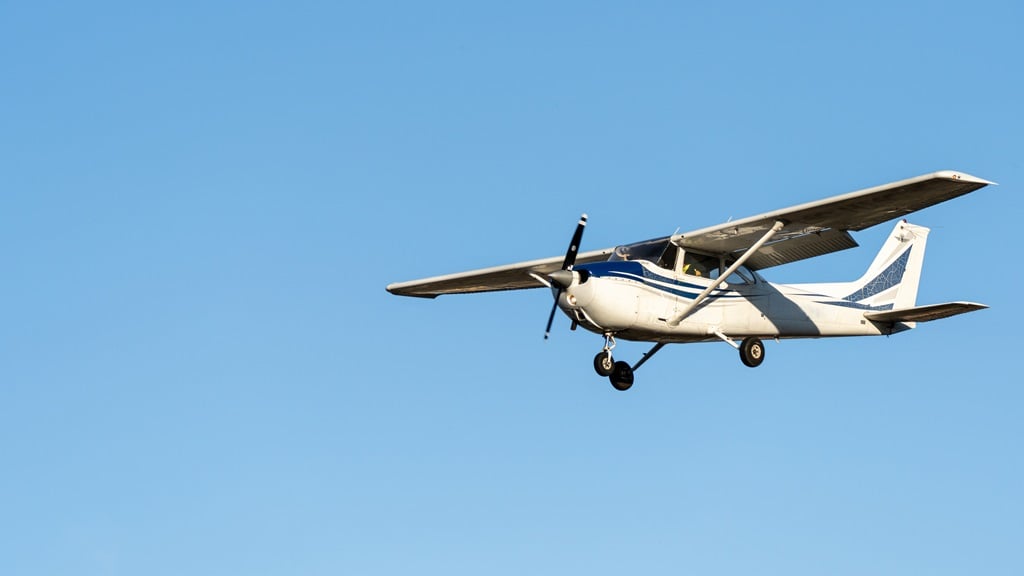
The EVS 100 achieved FAA certification, and the industry’s response was overwhelmingly positive. Demand quickly grew, and Max-Viz’s Enhanced Vision Systems was acquired by Astronics Corporation. Max-Viz Enhanced Vision Systems continue to provide pilots with an affordable solution that “turns night into day®”, improve visibility through dust, smoke or poor weather conditions and have now been certified on more than 200 aircraft models.
Conclusion
At Sherpa Design, we pride ourselves on our collaborative, innovative, and resourceful approach. Working hand-in-hand with Max-Viz, we helped them transform their vision of enhancing pilot visibility into a reality. Together, we overcame design challenges, optimized manufacturing processes, and achieved remarkable results.
Whether it’s developing groundbreaking thermal camera systems or implementing cutting-edge technologies, our team is here to partner with you on your engineering journey. Let’s reach new heights together.