On-Demand Small-Batch Production
The goal for our collaboration with KC Headsets was to improve the durability of their yokes. One part that had previously been injection-molded didn’t hold up as well as their standards required. What’s more, they were expensive and difficult to source. KC Headsets saw this as an opportunity to manufacture their own replacement parts with Carbon 3D printing technology — perfect for its low up-front cost and the ability to produce small batches on demand.
Solving the Root Cause of Fractures
Our team at Sherpa used NX CAD to reverse-engineer the part and optimize it for Carbon 3D printing. In the process, we found that some of the features on the original were solely intended for reducing injection molding sink. Those features were stress concentrations and frequently caused fracturing under load. We filled in those features and never received reports of fracturing after that change.
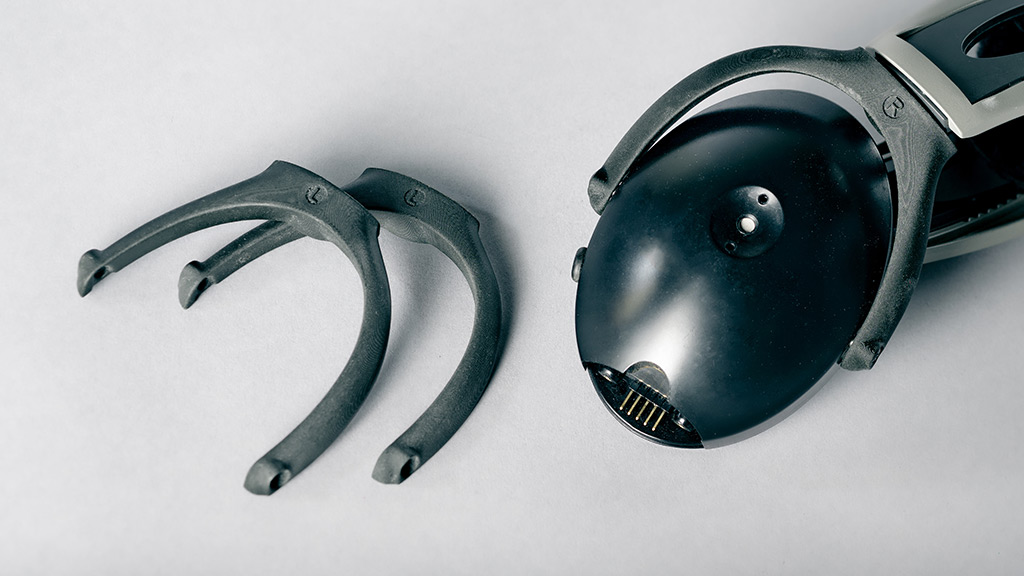
Quick and Seamless Iterations
Without the restriction of hard tooling, we were able to iterate designs quickly based on initial testing feedback and then manufacture the new versions. We even completed a material change without any hiccups.
Now the first third-party retailer of replacement parts, KC Headsets has shipped more than 1,500 parts using our fast, on-demand 3D printing technology.
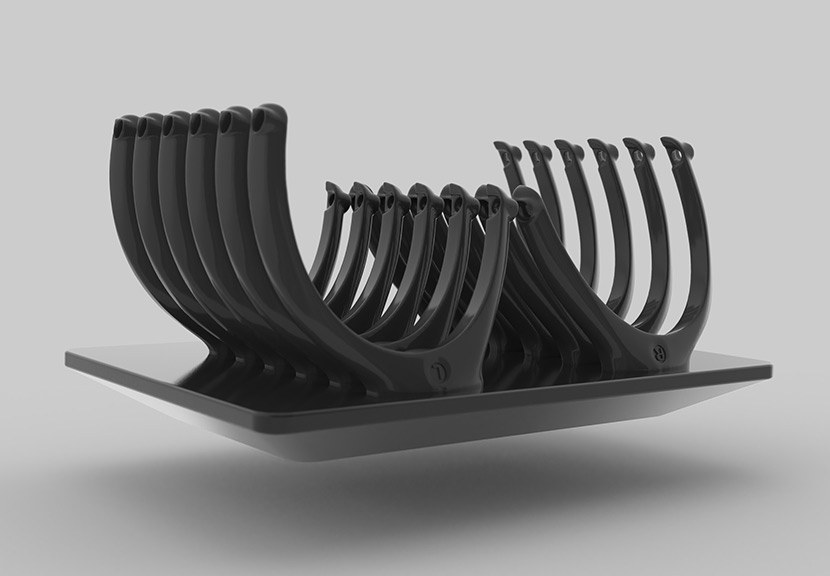
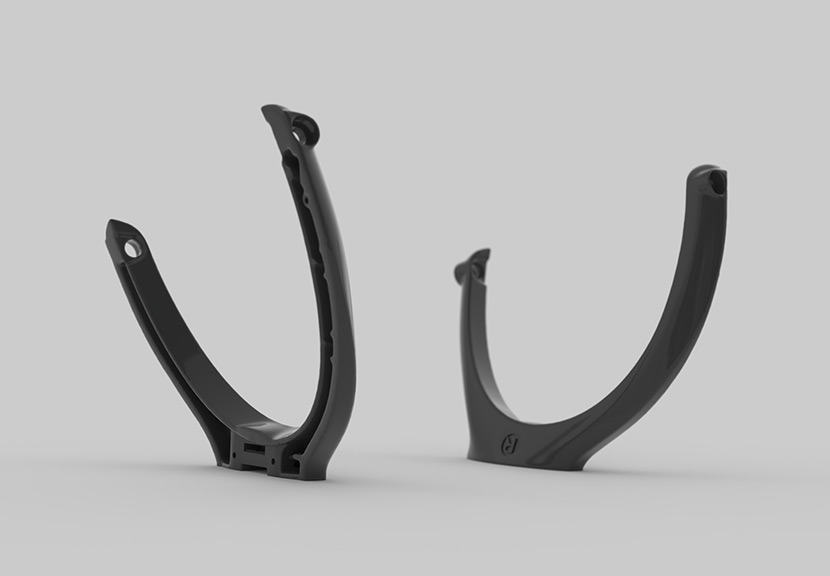
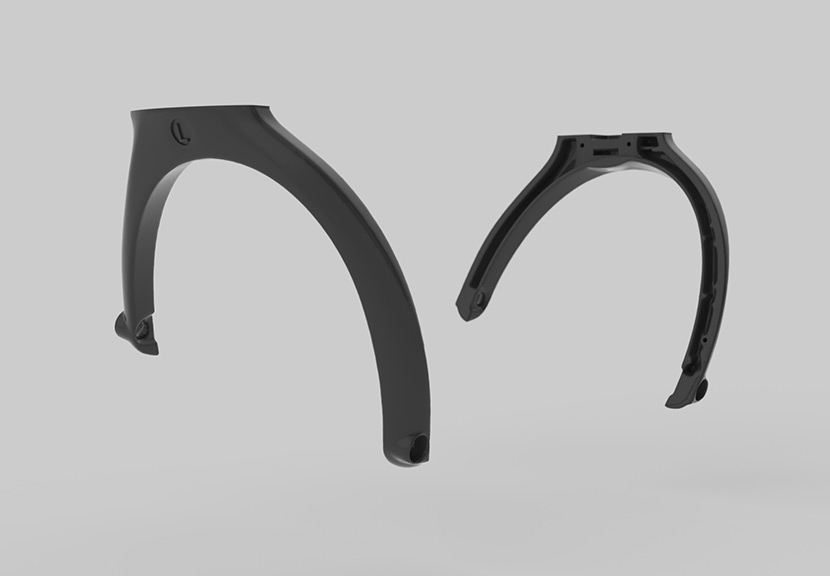